The level of resistance to abrasion and wear varies among different tubing materials used in gear pumps due to differences in material properties, composition, and manufacturing processes. Here’s how it typically varies:
- Rubber Materials (e.g., Nitrile, EPDM):
- Rubber materials offer moderate resistance to abrasion and wear, making them suitable for handling fluids with low to moderate levels of abrasiveness.
- Nitrile rubber, for example, provides good resistance to oils, fuels, and hydraulic fluids, but it may wear more quickly when exposed to abrasive particles or harsh chemicals.
- EPDM rubber offers better resistance to ozone, weathering, and environmental degradation but may exhibit lower resistance to oil and chemical exposure.
- Polyurethane:
- Polyurethane tubing offers higher abrasion resistance compared to rubber materials due to its superior wear properties and toughness.
- Polyurethane is often used in applications where tubing is subjected to high levels of mechanical wear or abrasive media, such as slurries, abrasives, gear pumps or granular materials.
- Polyurethane tubing can withstand repeated flexing and bending without significant degradation, making it suitable for dynamic applications in gear pumps.
- PVC (Polyvinyl Chloride):
- PVC tubing provides moderate resistance to abrasion and wear and is commonly used in applications where chemical resistance and cost-effectiveness are priorities.
- While PVC tubing may exhibit good resistance to certain chemicals and fluids, it may wear more quickly when exposed to abrasive particles or high-velocity flows.
- Reinforced PVC tubing, with added layers or braiding for increased strength and durability, offers improved resistance to abrasion and wear compared to standard PVC tubing.
- Fluoropolymer (e.g., PTFE, FEP):
- Fluoropolymer tubing, such as PTFE (polytetrafluoroethylene) or FEP (fluorinated ethylene propylene), offers excellent resistance to abrasion, wear, and chemical attack.
- Fluoropolymer materials are highly inert and non-reactive, making them suitable for handling corrosive fluids, solvents, and aggressive chemicals.
- PTFE tubing, in particular, is known for its low coefficient of friction and non-stick properties, which minimize wear and frictional losses in gear pump applications.
- Metal (e.g., Stainless Steel, Brass):
- Metal tubing, such as stainless steel or brass, offers superior resistance to abrasion and wear compared to polymer materials.
- Metal tubing is often used in applications where high mechanical strength, durability, and resistance to extreme temperatures and pressures are required.
- Stainless steel tubing, for example, is highly resistant to corrosion, erosion, and wear, making it suitable for handling abrasive fluids or high-temperature environments.
In summary, the level of resistance to abrasion and wear varies among different tubing materials used in gear pumps, with materials like polyurethane and fluoropolymers offering higher resistance compared to rubber or PVC. The selection of tubing material depends on factors such as the abrasiveness of the fluid being pumped, operating conditions, chemical compatibility, and cost considerations.
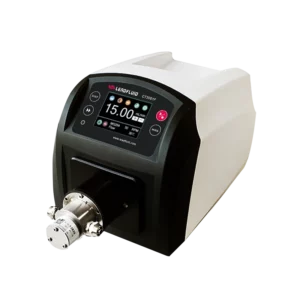